Metal extraction is a vital process in industrial chemistry, converting raw mineral ores into usable metallic elements. Metals play an essential role across multiple sectors, including construction, electronics, healthcare, and transportation. This guide explores the fundamental principles, methods of extraction of metals, and technologies involved in extracting metals, organized according to their reactivity and natural occurrence.
What Is Metal Extraction?
Metal extraction refers to the process of obtaining pure metals from their naturally occurring sources, known as ores. Ores are mineral-rich rocks that contain metals in combined forms, usually as oxides, sulfides, or carbonates. Before a metal can be used, it must be separated from these compounds through physical and chemical methods.
Types of Ores and Their Importance
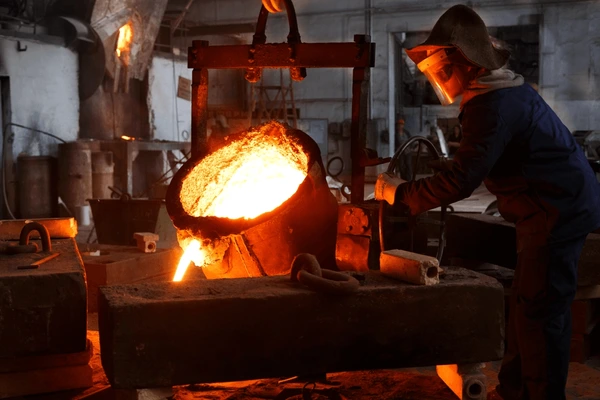
Metals are extracted from various ores, which are naturally occurring rocks containing metal compounds. Common types of ores include:
- Oxide Ores (e.g., bauxite for aluminum, hematite for iron)
- Sulfide Ores (e.g., galena for lead, zinc blende for zinc)
- Carbonate Ores (e.g., calcite for calcium)
The nature of the ore significantly influences the extraction method. Oxide ores are generally easier to reduce compared to sulfides and carbonates.
Reactivity Series and Its Role in Extraction
The reactivity series classifies metals according to how they react with oxygen, water, acids, and other substances. It is essential in selecting the appropriate method for metal extraction.
- Highly reactive metals (e.g., potassium, sodium, calcium, magnesium, aluminum) are extracted by electrolysis.
- Moderately reactive metals (e.g., zinc, iron, tin, lead) are extracted by chemical reduction using carbon or carbon monoxide.
- Less reactive metals (e.g., gold, silver, platinum) are found in their native state and require minimal extraction processes.
Extraction Methods Based on Reactivity
1. Electrolysis for Reactive Metals
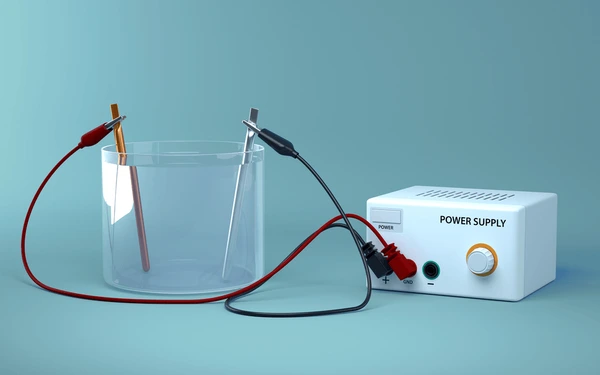
Electrolysis is used for metals high in the reactivity series that cannot be reduced by carbon. In this method:
- The metal ore is first converted into a molten or aqueous ionic form.
- An electric current is passed through the electrolyte.
- Pure metal is deposited at the cathode.
Example: Extraction of aluminum from bauxite (Al₂O₃)
Aluminum is extracted through the electrolysis of molten aluminum oxide, which is dissolved in cryolite to reduce its melting point and enhance electrical conductivity.
Equation: Al₂O₃ (l) → 2Al³⁺(l) + 3O²⁻(l)
2. Reduction with Carbon for Moderately Reactive Metals
Carbon reduction is cost-effective and widely used for extracting metals like iron, zinc, and lead. The process involves:
- Heating the metal oxide with carbon or carbon monoxide.
- Carbon acts as a reducing agent, removing oxygen from the metal oxide.
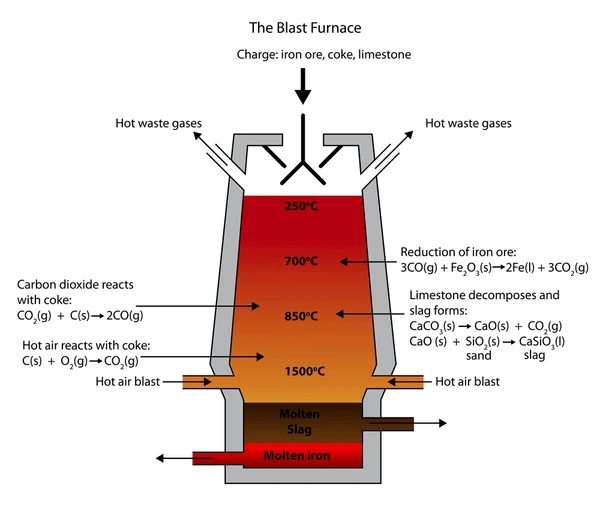
Example: Obtaining iron from hematite (Fe₂O₃)
In a blast furnace, iron ore is reduced using coke and limestone.
Equation: Fe₂O₃ + 3C → 2Fe + 3CO
3. Roasting and Smelting for Sulfide Ores
Sulfide ores are first roasted in air to convert them into oxides before reduction.
Example: Extraction of zinc from zinc blende (ZnS)
- Roasting step:
2ZnS+3O₂→2ZnO+2SO₂ - Reduction step:
ZnO + C → Zn + CO
This process releases sulfur dioxide gas, so environmental controls are essential.
4. Physical Methods for Native Metals
Metals like gold and silver, found in the elemental state, are separated using physical methods such as:
- Panning
- Hydraulic washing
- Froth flotation (for complex ores)
These processes involve gravity separation, density differences, or flotation agents that bind to metal particles.
Steps Involved in Metal Extraction
The general steps involved in metal extraction are:
1. Mining
- Ores are mined from open-pit or underground mines.
- Requires crushing and grinding to increase surface area.
2. Concentration of Ore
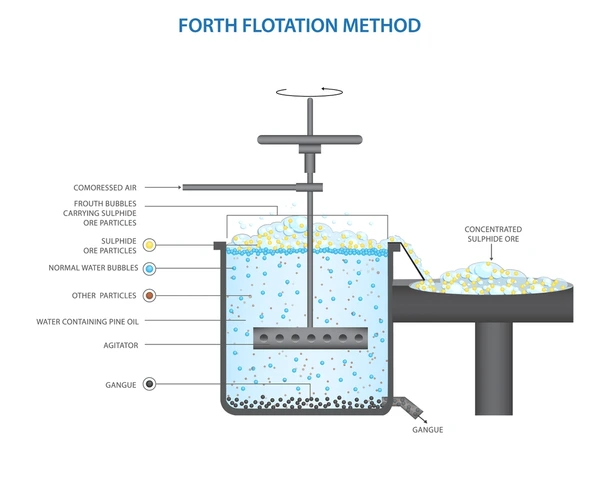
- Unwanted impurities (gangue) are removed.
- Methods include froth flotation, magnetic separation, and gravity separation.
3. Extraction of Metal
- The actual process is to isolate metal using chemical or electrochemical techniques.
4. Refining
- The extracted metal is purified using methods like:
- Electrolytic refining
- Distillation
- Liquation
Environmental Impact of Metal Extraction
The extraction of metals has significant environmental implications, including:
- Air pollution (due to release of SO₂, CO₂)
- Water contamination from mine runoff
- Habitat destruction from mining activities
- Energy consumption in electrolysis and smelting
Mitigation involves:
- Use of sustainable mining practices
- Recycling of metals
- Waste management strategies
Methods of Metal Extraction
Reactivity Level | Examples | Extraction Method |
---|---|---|
High | Sodium, Aluminum | Electrolysis |
Moderate | Iron, Zinc | Chemical Reduction |
Low | Gold, Silver | Physical Methods |
Advantages of Recycling Metals
Recycling plays an essential role in conserving natural resources and minimizing environmental impact. Its main benefits include:
- Energy savings (recycling aluminum saves up to 95% of energy)
- Reduction in greenhouse gases
- Lower mining demand
- Preservation of biodiversity
Metals like aluminum, copper, and steel are highly recyclable and retain their properties.
Modern Trends in Metal Extraction
The industry is moving towards eco-friendly technologies such as:
- Bioleaching – using bacteria to extract metals from ores
- Phytomining – using plants to absorb metals from the soil
- Hydrometallurgy – metal extraction using aqueous solutions
These techniques are designed to minimize environmental harm while lowering operational expenses.
Conclusion
The extraction of metals is a cornerstone of modern civilization, enabling the production of materials that fuel our infrastructure, technology, and daily life. From traditional carbon reduction to cutting-edge bioleaching, understanding these processes equips us to innovate sustainably. With environmental awareness on the rise, the future of metal extraction lies in green technologies, efficient recycling, and smart resource management.
As technology advances, scientists are continually looking for greener, more efficient ways to extract metals. This not only helps protect the environment but also ensures that we can sustainably meet future demands.
What are the steps of the extraction of metals?
1. Electrolysis for Reactive Metals
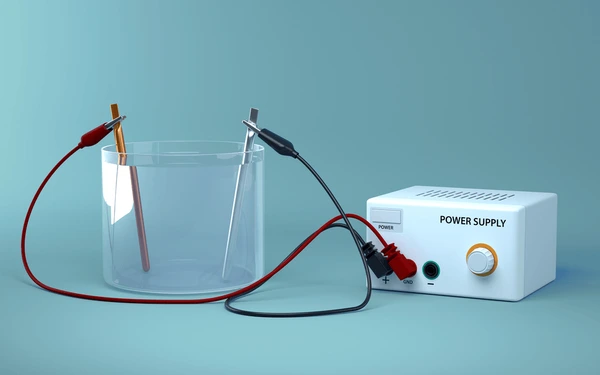
Electrolysis is used for metals high in the reactivity series that cannot be reduced by carbon. In this method:
The metal ore is first converted into a molten or aqueous ionic form.
An electric current is passed through the electrolyte.
Pure metal is deposited at the cathode.
Example: Extraction of aluminum from bauxite (Al₂O₃)
Aluminum is extracted through the electrolysis of molten aluminum oxide, which is dissolved in cryolite to reduce its melting point and enhance electrical conductivity.
Equation: Al₂O₃ (l) → 2Al³⁺(l) + 3O²⁻(l)
2. Reduction with Carbon for Moderately Reactive Metals
Carbon reduction is cost-effective and widely used for extracting metals like iron, zinc, and lead. The process involves:
Heating the metal oxide with carbon or carbon monoxide.
Carbon acts as a reducing agent, removing oxygen from the metal oxide.
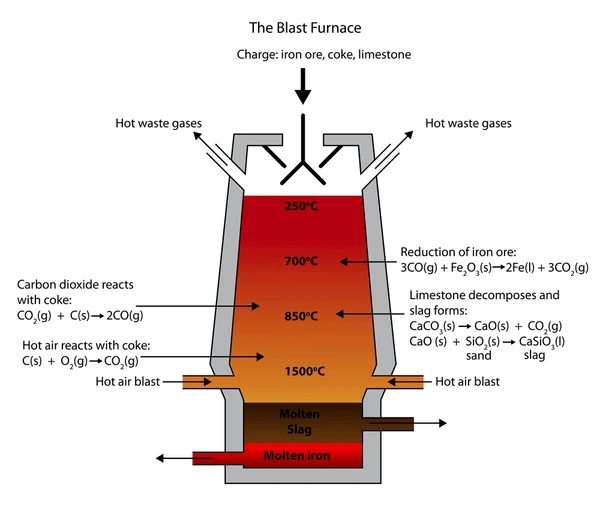
Example: Obtaining iron from hematite (Fe₂O₃)
In a blast furnace, iron ore is reduced using coke and limestone.
Equation: Fe₂O₃ + 3C → 2Fe + 3CO
3. Roasting and Smelting for Sulfide Ores
Sulfide ores are first roasted in air to convert them into oxides before reduction.
Example: Extraction of zinc from zinc blende (ZnS)
Roasting step:
2ZnS+3O₂→2ZnO+2SO₂
Reduction step:
ZnO + C → Zn + CO
This process releases sulfur dioxide gas, so environmental controls are essential.
4. Physical Methods for Native Metals
Metals like gold and silver, found in the elemental state, are separated using physical methods such as:
Panning
Hydraulic washing
Froth flotation (for complex ores)
These processes involve gravity separation, density differences, or flotation agents that bind to metal particles.
Steps Involved in Metal Extraction
The general steps involved in metal extraction are:
1. Mining
Ores are mined from open-pit or underground mines.
Requires crushing and grinding to increase surface area.
2. Concentration of Ore
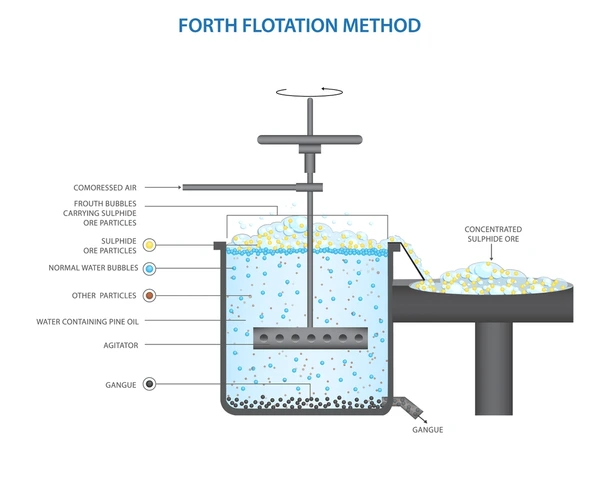
Unwanted impurities (gangue) are removed.
Methods include froth flotation, magnetic separation, and gravity separation.
3. Extraction of Metal
The actual process is to isolate metal using chemical or electrochemical techniques.
4. Refining
The extracted metal is purified using methods like: Electrolytic refining
Distillation
Liquation
What is the extraction of metals?
Extraction of metals refers to the process of obtaining pure metals from their naturally occurring sources, known as ores. Ores are mineral-rich rocks that contain metals in combined forms, usually as oxides, sulfides, or carbonates. Before a metal can be used, it must be separated from these compounds through physical and chemical methods.
Types of Ores and Their Importance
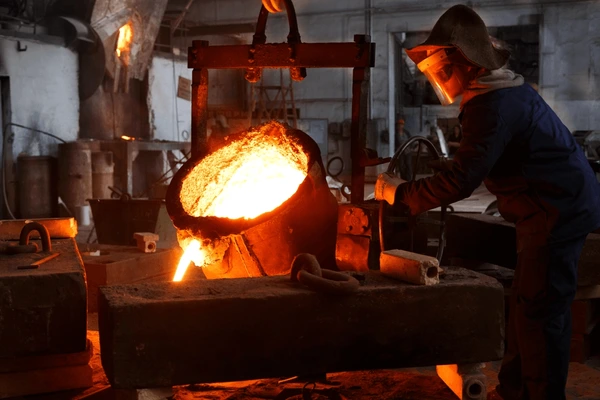
Metals are extracted from various ores, which are naturally occurring rocks containing metal compounds. Common types of ores include:
Oxide Ores (e.g., bauxite for aluminum, hematite for iron)
Sulfide Ores (e.g., galena for lead, zinc blende for zinc)
Carbonate Ores (e.g., calcite for calcium)
The nature of the ore significantly influences the extraction method. Oxide ores are generally easier to reduce compared to sulfides and carbonates.
Reactivity Series and Its Role in Extraction
The reactivity series classifies metals according to how they react with oxygen, water, acids, and other substances. It is essential in selecting the appropriate method for metal extraction.
Highly reactive metals (e.g., potassium, sodium, calcium, magnesium, aluminum) are extracted by electrolysis.
Moderately reactive metals (e.g., zinc, iron, tin, lead) are extracted by chemical reduction using carbon or carbon monoxide.
Less reactive metals (e.g., gold, silver, platinum) are found in their native state and require minimal extraction processes.
Extraction Methods Based on Reactivity
1. Electrolysis for Reactive Metals
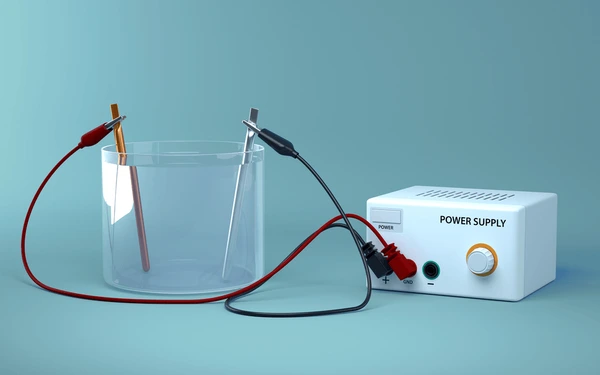
Electrolysis is used for metals high in the reactivity series that cannot be reduced by carbon. In this method:
The metal ore is first converted into a molten or aqueous ionic form.
An electric current is passed through the electrolyte.
Pure metal is deposited at the cathode.
Example: Extraction of aluminum from bauxite (Al₂O₃)
Aluminum is extracted through the electrolysis of molten aluminum oxide, which is dissolved in cryolite to reduce its melting point and enhance electrical conductivity.
Equation: Al₂O₃ (l) → 2Al³⁺(l) + 3O²⁻(l)
2. Reduction with Carbon for Moderately Reactive Metals
Carbon reduction is cost-effective and widely used for extracting metals like iron, zinc, and lead. The process involves:
Heating the metal oxide with carbon or carbon monoxide.
Carbon acts as a reducing agent, removing oxygen from the metal oxide.
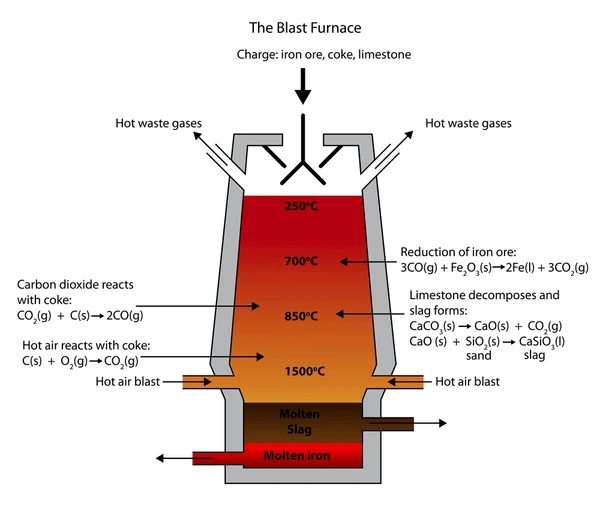
Example: Obtaining iron from hematite (Fe₂O₃)
In a blast furnace, iron ore is reduced using coke and limestone.
Equation: Fe₂O₃ + 3C → 2Fe + 3CO
3. Roasting and Smelting for Sulfide Ores
Sulfide ores are first roasted in air to convert them into oxides before reduction.
Example: Extraction of zinc from zinc blende (ZnS)
Roasting step:
2ZnS+3O₂→2ZnO+2SO₂
Reduction step:
ZnO + C → Zn + CO
This process releases sulfur dioxide gas, so environmental controls are essential.
4. Physical Methods for Native Metals
Metals like gold and silver, found in the elemental state, are separated using physical methods such as:
Panning
Hydraulic washing
Froth flotation (for complex ores)
These processes involve gravity separation, density differences, or flotation agents that bind to metal particles.
Steps Involved in Metal Extraction
The general steps involved in metal extraction are:
1. Mining
Ores are mined from open-pit or underground mines.
Requires crushing and grinding to increase surface area.
2. Concentration of Ore
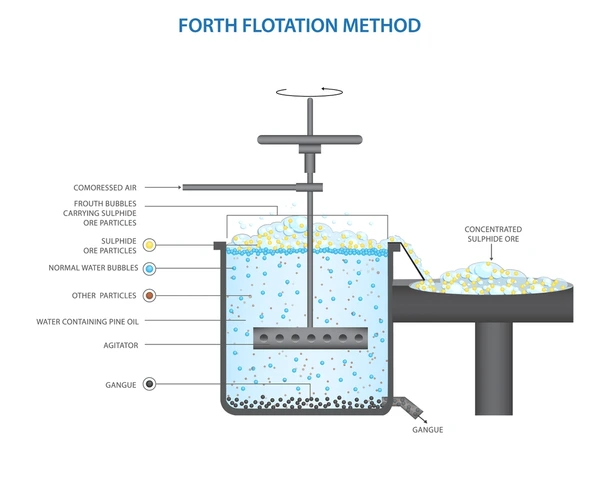
Unwanted impurities (gangue) are removed.
Methods include froth flotation, magnetic separation, and gravity separation.
3. Extraction of Metal
The actual process is to isolate metal using chemical or electrochemical techniques.
4. Refining
The extracted metal is purified using methods like: Electrolytic refining
Distillation
Liquation
Environmental Impact of Metal Extraction
The extraction of metals has significant environmental implications, including:
Air pollution (due to release of SO₂, CO₂)
Water contamination from mine runoff
Habitat destruction from mining activities
Energy consumption in electrolysis and smelting
Mitigation involves:
Use of sustainable mining practices
Recycling of metals
Waste management strategies
Methods of Metal Extraction
Reactivity Level | Examples | Extraction Method |
---|---|---|
High | Sodium, Aluminum | Electrolysis |
Moderate | Iron, Zinc | Chemical Reduction |
Low | Gold, Silver | Physical Methods |
Recycling plays an essential role in conserving natural resources and minimizing environmental impact. Its main benefits include:
Energy savings (recycling aluminum saves up to 95% of energy)
Reduction in greenhouse gases
Lower mining demand
Preservation of biodiversity
Metals like aluminum, copper, and steel are highly recyclable and retain their properties.
Modern Trends in Metal Extraction
The industry is moving towards eco-friendly technologies such as:
Bioleaching – using bacteria to extract metals from ores
Phytomining – using plants to absorb metals from the soil
Hydrometallurgy – metal extraction using aqueous solutions
These techniques are designed to minimize environmental harm while lowering operational expenses.
Conclusion
The extraction of metals is a cornerstone of modern civilization, enabling the production of materials that fuel our infrastructure, technology, and daily life. From traditional carbon reduction to cutting-edge bioleaching, understanding these processes equips us to innovate sustainably. With environmental awareness on the rise, the future of metal extraction lies in green technologies, efficient recycling, and smart resource management.
As technology advances, scientists are continually looking for greener, more efficient ways to extract metals. This not only helps protect the environment but also ensures that we can sustainably meet future demands.
What is the process of metal extraction?
The general steps involved in metal extraction are:
1. Mining
Ores are mined from open-pit or underground mines.
Requires crushing and grinding to increase surface area.
2. Concentration of Ore
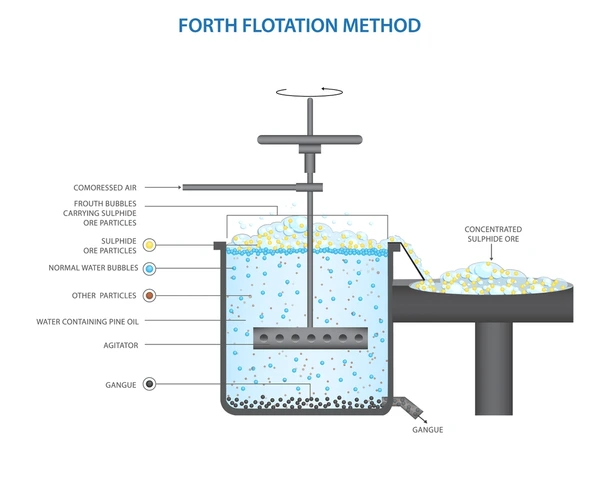
Unwanted impurities (gangue) are removed.
Methods include froth flotation, magnetic separation, and gravity separation.
3. Extraction of metals
The actual process is to isolate metal using chemical or electrochemical techniques.
4. Refining
The extracted metal is purified using methods like: Electrolytic refining
Distillation
Liquation
Environmental Impact on the Extraction of Metals
The extraction of metals has significant environmental implications, including:
Air pollution (due to the release of SO₂, CO₂)
Water contamination from mine runoff
Habitat destruction from mining activities
Energy consumption in electrolysis and smelting
Mitigation involves the extraction of metals
Use of sustainable mining practices
Recycling of metals
Waste management strategies
Methods of Extraction of Metals
Reactivity Level | Examples | Extraction Method |
---|---|---|
High | Sodium, Aluminum | Electrolysis |
Moderate | Iron, Zinc | Chemical Reduction |
Low | Gold, Silver | Physical Methods |
Explain the extraction of metals.
The extraction of metals is a vital process in industrial chemistry, converting raw mineral ores into usable metallic elements. Metals play an essential role across multiple sectors, including construction, electronics, healthcare, and transportation. This guide explores the fundamental principles, methods of extraction of metals, and technologies involved in extracting metals, organized according to their reactivity and natural occurrence.
Extraction of metals refers to the process of obtaining pure metals from their naturally occurring sources, known as ores. Ores are mineral-rich rocks that contain metals in combined forms, usually as oxides, sulfides, or carbonates. Before a metal can be used, it must be separated from these compounds through physical and chemical methods.
Extraction of metals
Types of Ores and Their Importance
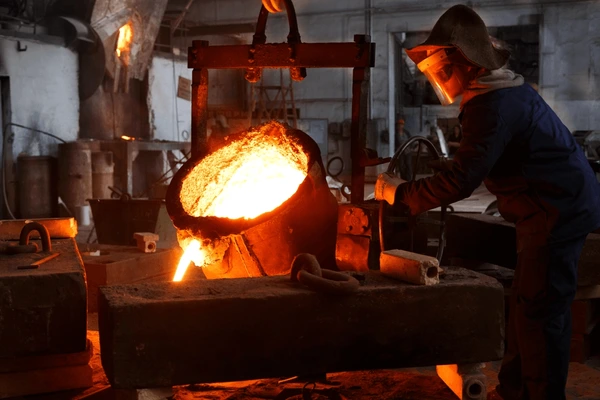
Metals are extracted from various ores, which are naturally occurring rocks containing metal compounds. Common types of ores include:
Oxide Ores (e.g., bauxite for aluminum, hematite for iron)
Sulfide Ores (e.g., galena for lead, zinc blende for zinc)
Carbonate Ores (e.g., calcite for calcium)
The nature of the ore significantly influences the extraction method. Oxide ores are generally easier to reduce compared to sulfides and carbonates.
Reactivity Series and Its Role in Extraction of metals
The reactivity series classifies metals according to how they react with oxygen, water, acids, and other substances. It is essential in selecting the appropriate method for metal extraction.
Highly reactive metals (e.g., potassium, sodium, calcium, magnesium, aluminum) are extracted by electrolysis. Extraction of metals
Moderately reactive metals (e.g., zinc, iron, tin, lead) are extracted by chemical reduction using carbon or carbon monoxide.
Less reactive metals (e.g., gold, silver, platinum) are found in their native state and require minimal extraction processes.
Extraction Methods Based on Reactivity
1. Electrolysis for Reactive Metals
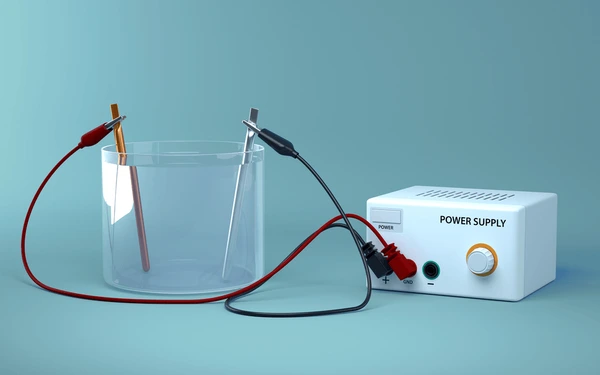
Electrolysis is used for metals high in the reactivity series that cannot be reduced by carbon. In this method:
The metal ore is first converted into a molten or aqueous ionic form.
An electric current is passed through the electrolyte.
Pure metal is deposited at the cathode.
Example: Extraction of aluminum from bauxite (Al₂O₃)
Aluminum is extracted through the electrolysis of molten aluminum oxide, which is dissolved in cryolite to reduce its melting point and enhance electrical conductivity.
Equation: Al₂O₃ (l) → 2Al³⁺(l) + 3O²⁻(l)
2. Reduction with Carbon for Moderately Reactive Metals
Carbon reduction is cost-effective and widely used for extracting metals like iron, zinc, and lead. The process involves:
Heating the metal oxide with carbon or carbon monoxide.
Carbon acts as a reducing agent, removing oxygen from the metal oxide.
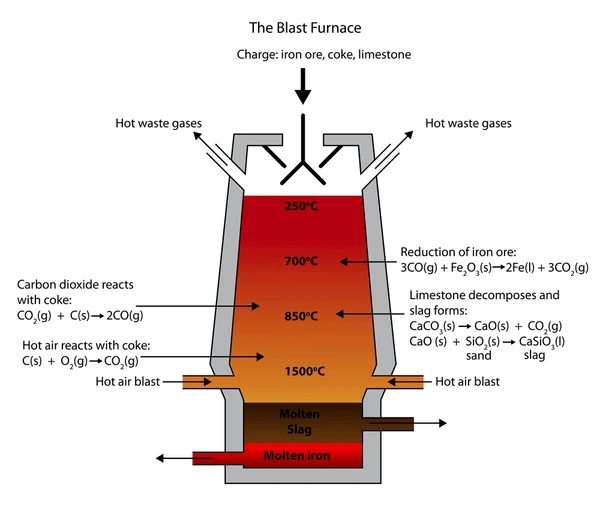
Example: Obtaining iron from hematite (Fe₂O₃)
In a blast furnace, iron ore is reduced using coke and limestone.
Equation: Fe₂O₃ + 3C → 2Fe + 3CO
3. Roasting and Smelting for Sulfide Ores
Sulfide ores are first roasted in air to convert them into oxides before reduction.
Example: Extraction of zinc from zinc blende (ZnS)
Roasting step:
2ZnS+3O₂→2ZnO+2SO₂
Reduction step:
ZnO + C → Zn + CO
This process releases sulfur dioxide gas, so environmental controls are essential.
4. Physical Methods for Native Metals
Metals like gold and silver, found in the elemental state, are separated using physical methods such as:
Panning
Hydraulic washing
Froth flotation (for complex ores)
These processes involve gravity separation, density differences, or flotation agents that bind to metal particles.
Steps Involved in the Extraction of Metals
The general steps involved in metal extraction are:
1. Mining
Ores are mined from open-pit or underground mines.
Requires crushing and grinding to increase surface area.
2. Concentration of Ore
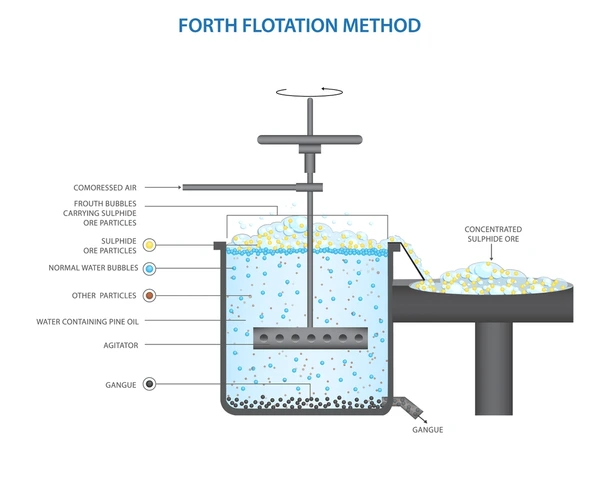
Unwanted impurities (gangue) are removed.
Methods include froth flotation, magnetic separation, and gravity separation.
3. Extraction of Metals
The actual process is to isolate metal using chemical or electrochemical techniques.
4. Refining
The extracted metal is purified using methods like: Electrolytic refining
Distillation
Liquation
Environmental Impact of Extraction of Metals
The extraction of metals has significant environmental implications, including:
Air pollution (due to release of SO₂, CO₂)
Water contamination from mine runoff
Habitat destruction from mining activities
Energy consumption in electrolysis and smelting
Mitigation involves:
Use of sustainable mining practices
Recycling of metals
Waste management strategies, Extraction of metals
Methods of Extraction of metals
Reactivity Level | Examples | Extraction Method |
---|---|---|
High | Sodium, Aluminum | Electrolysis |
Moderate | Iron, Zinc | Chemical Reduction |
Low | Gold, Silver | Physical Methods |
Recycling plays an essential role in conserving natural resources and minimizing environmental impact. Its main benefits include:
Energy savings (recycling aluminum saves up to 95% of energy)
Reduction in greenhouse gases
Lower mining demand
Preservation of biodiversity
Metals like aluminum, copper, and steel are highly recyclable and retain their properties.
Modern Trends in Extraction of Metals
The industry is moving towards eco-friendly technologies such as:
Bioleaching – using bacteria to extract metals from ores
Phytomining – using plants to absorb metals from the soil
Hydrometallurgy – metal extraction using aqueous solutions
These techniques are designed to minimize environmental harm while lowering operational expenses.
Conclusion
The extraction of metals is a cornerstone of modern civilization, enabling the production of materials that fuel our infrastructure, technology, and daily life. From traditional carbon reduction to cutting-edge bioleaching, understanding these processes equips us to innovate sustainably. With environmental awareness on the rise, the future of metal extraction lies in green technologies, efficient recycling, and smart resource management.
As technology advances, scientists are continually looking for greener, more efficient ways to extract metals. The extraction of metals not only helps protect the environment but also ensures that we can sustainably meet future demands.